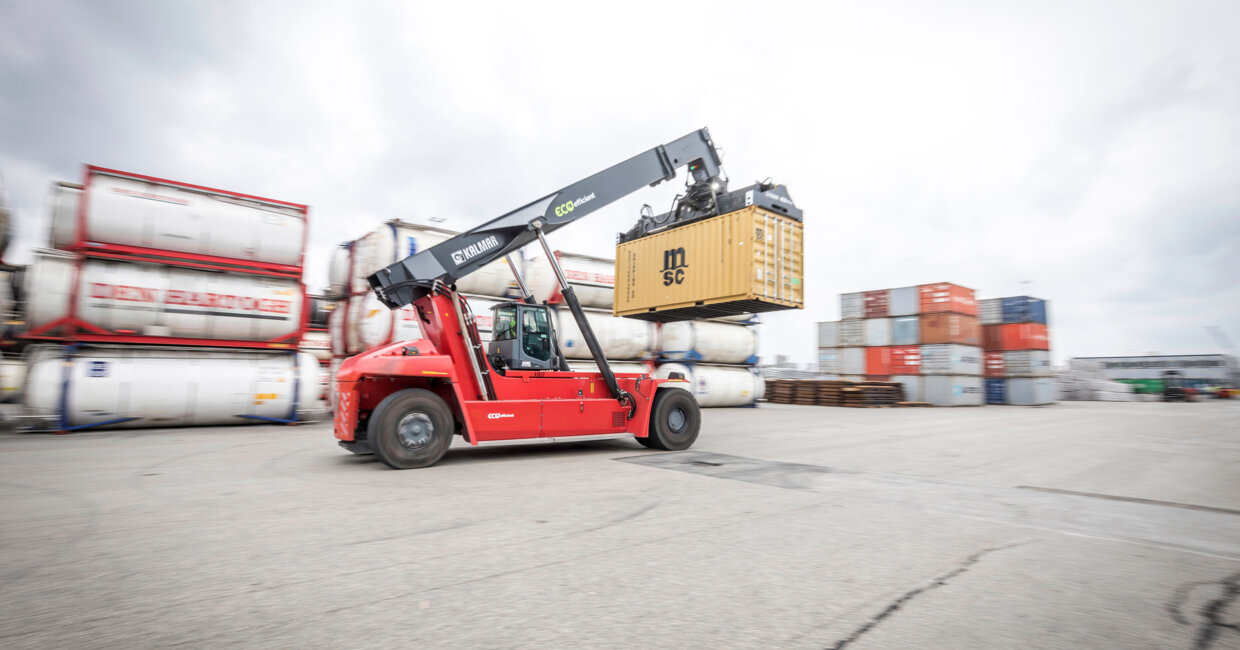
How to become greener with your reachstacker operations?
With Covid-19 induced downtime in cargo handling operations, now is the perfect time to optimize your emissions and energy efficiency. Peter Olsson and Mette Kjems Bærentzen from Kalmar show how to transform your reachstacker operations towards an eco-efficient future: step by step, from optimizing existing equipment and operations to which new equipment to invest in. The ultimate goal: Zero-emission equipment.
Still largely diesel-based cargo handling equipment involves a lot of CO2 emissions. Looking at emission distribution in container terminals, port equipment – such as reachstackers and empty container handlers – grab a quarter (24%) of the total emissions. Globally speaking, one out of four container movements is performed by Kalmar equipment – meaning, in essence, that by making these operations as zero-emission as possible will have a considerable impact on the big picture.
“Luckily, eco-efficiency is becoming the standard in cargo handling operations,” says Mette Kjems Bærentzen, but she still warns against complacency. “We have to turn every stone to find ways to reduce CO2.”
Kalmar will launch an electric reachstacker at the end of 2021.
As a response to new, greener trends, the Zero Emission market in cargo handling is growing. Kalmar, for instance, will launch an electric reachstacker at the end of 2021.
“Slowly but surely, we’re getting electrified in more and more parts of the supply chain,” says Peter Olsson, adding that this, however, is an evolution that will take time – especially with regards to the heavy cargo handling equipment where investments are bigger.
Future is electric
Challenges against electrification include issues such as implementation cost, availability and grid capacity – in addition to the “usual suspects” battery power, charging, technology and infrastructure.
“There’s no doubt that the electrification journey will happen, but it will take time before it’s fully commercialized across the globe,“ Olsson says. Currently, with diesel, one way to proceed is updating one’s fleet to newer machines with more fuel-efficient drivelines.
One stellar example of this “greener hardware” is the Kalmar Eco Reachstacker which is guaranteed to reduce fuel consumption. Bærentzen notes that the company has spent 6-7 years developing new, greener versions of diesel-driven reachstacker with substantially reduced fuel consumption.
“The Kalmar Eco Reachstacker outperforms every other reachstacker in the market in terms of productivity versus fuel consumption,” she says.
Cut your fuel costs in half?
Easy enough measures, such as adapting your power consumption to actual productivity need and training operators in eco-efficient driving behavior, can get you considerable savings. Peter Olsson provides an example on how the “total package” of eco-actions can impact reachstacker operations.
“When you add it all up, there’s a possibility to save up to 40% in fuel cost alone,” he says.
For instance, idling is big “under the radar” problem as idling constitutes around 30% of all running hours. Eliminating or reducing idling will, naturally, bring in big savings in fuel cost, notes Olsson.
"There’s a possibility to save up to 40% in fuel cost alone."
Olsson also believes that eco-driving training for reachstacker operators is a “golden opportunity” to secure even more savings and one that should not be overlooked. With Kalmar reachstackers, learning how to drive according to actual productivity need and making the most of Kalmar's Eco Drive Mode functionality, for example, is an investment that will pay itself back very quickly in terms of both lower fuel cost as well as reduced wear and tear.
Last decade of diesel
Mette Kjems Bærentzen points out that the number of diesel reachstackers on the field is expected to drop once the Zero Emission reachstackers enter the game.
“Possibly - and hopefully - it will be around the year 2031 when there will be more zero emission reachstackers in the field than diesel reachstackers.”
The current impact of reachstackers is 2.5 million tons of CO2 annually, but using the “green means” alone can bring it under 2 million quite efficiently – while waiting for the cavalry (in the form of Zero Emission equipment) to arrive.
Your 5 actions for greener reachstacker operations
1 Update fleet to newer machines with more fuel-efficient drivelines.
2 Upgrade existing fleet with fuel reducing options.
3 Adapt power consumption to actual productivity need.
4 Train operators in eco-efficient driving behavior.
5 Set, monitor, visualize and follow-up CO2 reducing targets.
Peter Olsson and Mette Kjems Bærentzen gave tips on how to become greener with your reachstacker operations in a webinar hosted by Kalmar in June 2020 – a recording of the webinar is available at https://www.kalmarglobal.com/news--insights/webinars/Greener-with-Eco-RST/
Related articles
Subscribe and receive updates in your email
Subscribe