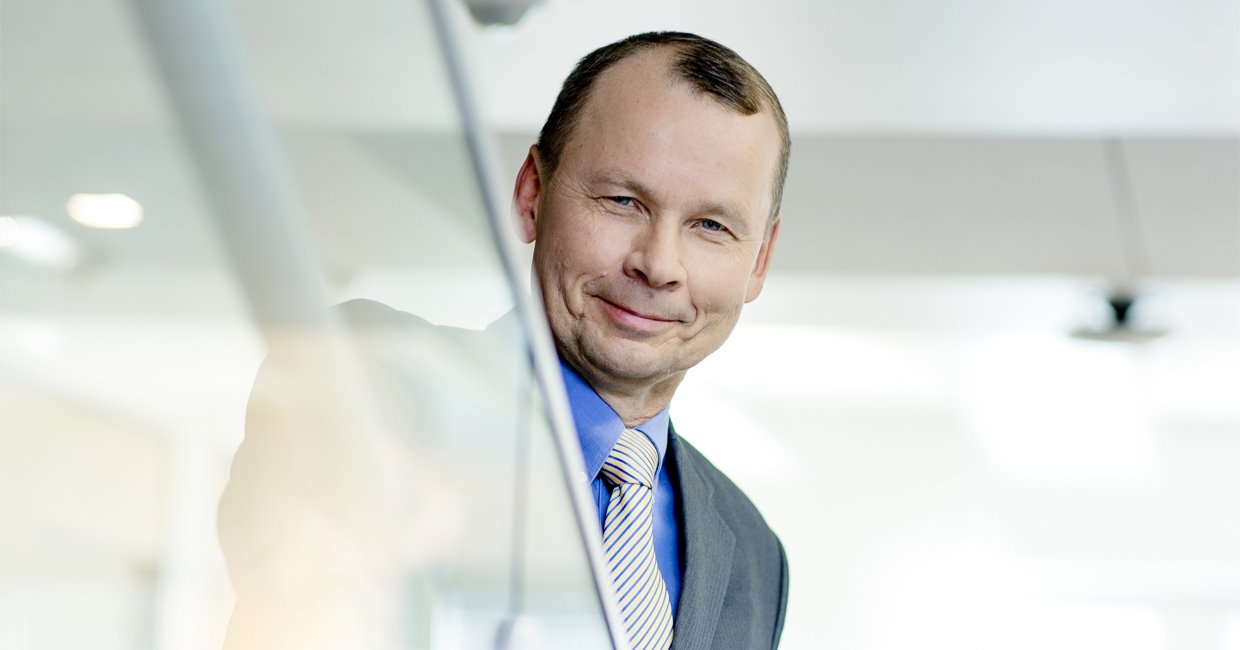
Safety at the heart of business
Improving occupational safety at container terminals calls for culture change, new technical solutions and industry-wide standardisation.
“Safety first” is a phrase that is commonly heard in almost any field of industry. But what does it mean in practice?
To me, safety simply means that everyone gets to go home to their families and friends after a day’s work. A fundamental safety challenge in the industry that we serve – container handling – is that accidents, when they happen, can be extremely serious due to the heavy equipment and large workloads involved. Typical incidents also involve hand injuries as well as people slipping on oily surfaces or when entering or exiting container handling machines.
The first step in improving occupational safety is actually measuring it regularly. This may sound obvious, but it is no easy task, especially in large companies with a global organisation and multiple business lines. Once you know the current situation, the second step is defining a target level and creating a company culture to achieve and maintain it.
At Kalmar, our goal for employee safety is five accidents per 1,000,000 working hours, which is an appropriate level for a professional company such as ours. My personal target is of course zero, but unfortunately some accidents are bound to happen once in a while in a large company like ours.
What does an accident rate of five incidents per 1,000,000 working hours mean? In numbers, it translates to one accident per year for every 600 employees. In practical terms, it means that if your field operations are done right, you will see more accidents in your back office than in your container yard.
On a side note: When you see people juggling their coffee cups, smart phones, laptops and notepaper while going up or down the stairs in the office, it does occur that some safety standards might be a good idea here as well. For decades, factories have had strict rules mandating that people keep at least one hand on the railing at all times when going down stairs. Maybe we could learn something from this?
Paradoxically, when defining the target accident rates for your company, you want to have a goal that is demanding – but not too low. Why? Because having an unrealistically low target level will tend to result in accidents not being reported when they do happen, especially if clean workplace safety records are tied to employee and management bonuses (which in itself can be a very good idea).
Occupational safety always goes hand in hand with the general culture of the company. If your safety records are good, the rest of your operations will very likely be well organised too, and vice versa. Similarly, if your own workplace safety is not exemplary, how can you hope to improve that of your customers?
In addition to organisational culture, a key way to improve safety is through technical solutions. In particular, automated terminals enable near-zero accidents simply by separating people from container handling equipment. At terminals that have converted to automation, the reduction in measured accident rates has been dramatic. The gains are also financial as safer terminals benefit from lower insurance premiums and reduced compensation costs.
Even at manually operated or semiautomated terminals, support systems and technical solutions play a key part in keeping both employees and external personnel safe. The safety system may involve extensive automation, sensoring and location-based technologies, or it can be as simple as requiring truck drivers to exit the vehicle cabin and press a physical button some distance away to authorise a container move onto the flatbed trailer.
Automation is the obvious way for terminals around the world to improve not only their safety, but also their productivity and performance. A major challenge at this time is that there are still no global safety standards for automated container terminals, or autonomously operating industrial equipment in general. Each country will have its own set of regulations, which often leave room for interpretation, so every solution is to some degree unique.
With terminals unsure of what they actually need and system providers hoping for more exact specifications from their clients, the lack of global standards in this field is slowing down everyone. If terminal operators and regulators are able to get together and define their needs, system providers will be able to deploy proven, standardised solutions faster and more efficiently, ultimately helping more employees go home safely at the end of the day.
Antti Kaunonen
President
Kalmar
Related articles
Further reading
Subscribe and receive updates in your email
Subscribe